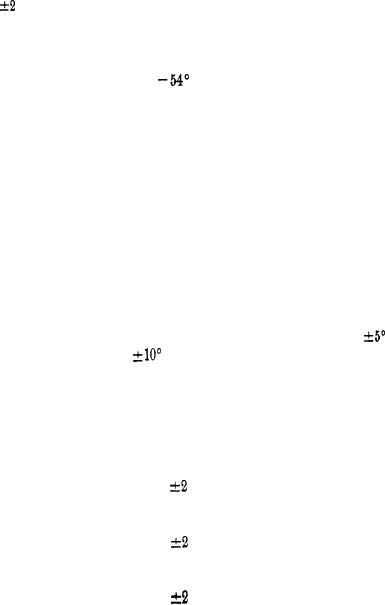
MIL-U-3963A
angularity and the torque specified in table 1,
specimens so that no drops of solution from
phase II, for an "ON" period of 40 seconds
specimens or other sources will be collected.
(1,000 revaluations) and an "OFF" period
Step 3. Repeat endurance test in step 1,
minimum time of 15 seconds for a total of
phase II.
100,000 revolutions.
Step 4. Altitude and humidity test. The
Step 2. Salt spray. test. The joints shall be
joints shall be rotated in the test chamber at 3
rotated in the test chamber at 3 rpm, with the
rpm, with the angle "An as shown in figure 1
angle "A" as shown on figure 1 equal to 20
equal to 20 degrees for a period of 16 hours.
degrees, for a period of 50 hours. The temper-
Throughout the test period, the relative humid-
ature in the test chamber shall be maintained
ity shall be maintained at a minimum of 95
at 35° C. (95° F.) throughout the test period.
percent and the pressure shall be varied con-
Salt solution. The salt used shall be sodium
forming to the following hourly cycle. A grad-
chloride containing on the dry basis not more
ual reduction during the initial 10 minutes from
than 0.1 percent of sodium iodide and not more
atmospheric pressure to between 30 to 20 inches
than 0.2 percent of total impurities. The solu-
Hg. The pressure shall then be maintained
tion shall be prepared by dissolving 20
parts
between 20 to 29 inches Hg for 50 minutes, fol-
by weight of salt in 80 parts by weight of dis-
lowed by a gradual pressure increase to atmos-
tilled or other water containing not more than
pheric during the final 5 minutes. During the
200 parts per million of total solids. The solu-
initial 8 hours, the temperature shall be main-
tion shall be kept free from solids by filtration
C. ( 65° F.). During the
tained at
or recantation. The solution shall be adjusted
final 8 hours, the temperature shall be main-
to and maintained at a specific gravity of from
tained at 71° C. ( 160° F.).
1.126 to 1.157 and at a pH of between 6.5 and 7.2
Step 5. Repeat endurance test outlined in
when measured at a temperature between 33°
step 1, phase II.
and 36° C. (92° and 97° F.). Only C.P. hydro-
Step 6. Sand and dust test. The joints shall
chloric acid or C.P. sodium hydroxide shall be
be rotated in the test chamber for 8 hours at
3 rpm with angle "A" shown on figure 1 equal
used to adjust the pH. The pH measurement
to 20 degrees and the sand and dust density
shall be made electrometrically using a glass
throughout the chamber shall be maintained
electrode with a saturated potassium chloride
between 0.1 and 0.5 grams per cubic foot. This
bridge or by a colormetric method such as
sand and dust velocity through the chamber
bromothymol blue, provided the results are
shall be maintained between 900 and 1,100 feet
equivalent to those obtained with the electro-
per minute. During this test, the test chamber
metric method.
temperature shall be maintained at 71°
C.
A tomization The conditions maintained in
(160°
F.).
all parts of the exposure zone shall be such that
Sand dust. The sand and dust used in the
a suitable receptacle placed at any point in the
test shall be of angular structure and shall have
exposure zone will collect from 0.5 to 3 ml of
characteristics as follows:
solution per hour for each 80 sq cm of hori-
(a) 100 percent of the sand and dust shall
zontal collecting area (10-cm diameter) based
pass through 100-mesh screen, U.S.
on an average of at least 16 hours. The solu-
Standard Sieve Series.
tion thus collected shall have a sodium chloride
(b) 98
percent of the sand and dust
content from 18 to 22 percent ( sp gr from
shall pass through a 140-mesh
1.126 to 1.157 when measured at a temperature
screen, U.S. Standard Sieve Series.
between 33° and 36° C. (91° and 97° F.)). At
(c) 90
percent of the sand and dust
least two clean fog collecting receptacles shall
shall pass through a 200-mesh screen,
be used, one placed nearest to any nozzle and
U.S. Standard Sieve Series.
one farthest from all nozzles. Receptacles shall
(d) 75
percent of the sand and dust
be so fastened that they are not shielded by
shall pass through a 325-mesh
6
For Parts Inquires call Parts Hangar, Inc (727) 493-0744
© Copyright 2015 Integrated Publishing, Inc.
A Service Disabled Veteran Owned Small Business