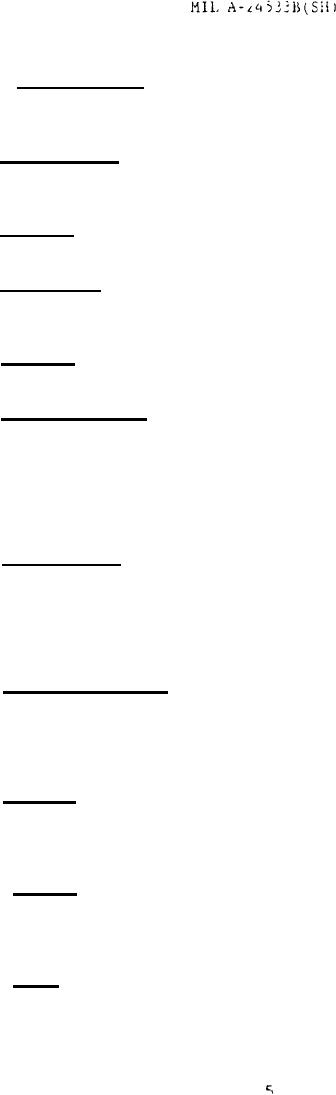
3 .4.1 1 Proof pressure. The actuator shall withstand a proof pressure of
1 5 times the design pressure with\out permanent deformation 01 external leakage
sufficient to form a drop
Unless otherwise specified (see 6.2), rotary actuators
3.4.2 Compatibility.
shall be compatible with the fluids identified in the compatibility requirements
of MIL-STD-2193,
3.4.3 Envelope.
Dimensions shall be within the envelope requirements of the
applicable specification sheet or as specified (see 6.2).
3.4 4 Orientation. Actuators shall operate in any orientation or position.
Actuator mounting bolt and dowel pin patterns shall meet the requirements of the
applicable specification sheets.
3,4.5 Rotation
The shaft rotating angle and its tolerance shall be in
accordance with the applicable specification sheet or as specified (see 6.2),
3.4.6 Operating cycles. The rotary actuator shall be designed to achieve a
minimum operating life of 50,000 cycles unless otherwise specified (see 6.2).
For two-position actuators, a cycle shall be defined as the shaft rotating from
one extreme position to the other and return. For three-position actuators, a
cycle shall be defined as the shaft rotating from the neutral position to one
extreme position and back to neutral, followed by rotation to the other extreme
position and return to neutral.
3.4.7 Output torque. Minimum and maximum output torques of the actuator at
the specified pressures shall be as established in the applicable specification
sheet. The minimum torque required shall be obtained at a differential pressure
not more than two-thirds the rated operating pressure. The maximum torque
developed at a differential pressure equal to the rated operating pressure shall
not exceed the minimum output torque specified by more than 175 percent.
3.4.8 Breakaway pressure. Differential pressure required to start motion of
the shaft in either direction under no-load conditions shall not exceed 100 pounds
per square inch (lb/in*)
Actuators shall comply with this requirement after
being held in either extreme position for at least 1 minute at the design
pressure.
3 4 9 Dashpots. When specified in the applicable specification sheet,
dashpots shall be designed to decelerate the motion of the piston near the end of
the stroke. The dashpot shall be adjustable and operate over approximately the
last 15 degrees of rotation, while meeting any applicable noise requirements.
3.4.10 Leakage. Actuator internal leakage shall not exceed the levels
specified in the applicable specification sheet under the operating and test
conditions specified herein. External leakage shall be insufficient to form a
drop under the same conditions
3,4.11 Seals
Seals, seal glands, and back-up rings shall be in accordance
with MIL-STD-2193
For Parts Inquires call Parts Hangar, Inc (727) 493-0744
© Copyright 2015 Integrated Publishing, Inc.
A Service Disabled Veteran Owned Small Business