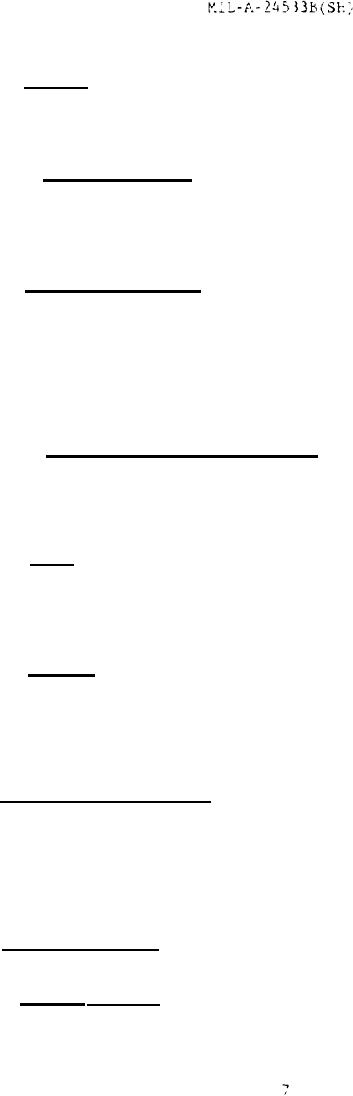
3.5.11 Gearing, Gearing, when required, shall be fully enclosed and shall
operate in an oil bath. Only spur gearing shall be used with material and design
Pinion gear and rack shall be match-marked for
in accordance with AGMA 390 03
proper assembly.
3.5.11.1 Case fluid level. Unless otherwise specified (see
6.2), the gear
case or main shaft cavity shall be filled with fluid as specified
in the applica-
ble specification sheet. An air space shall be provided to allow
for thermal
expansion of the fluid. If no fluid is identified, the gear case
shall be filled
with fluid in accordance with MIL-H-6083.
Unless otherwise specified (see 6.2), rotary
3.5.12 Position indication
actuators shall be complete with visual position indication. Remote electrical
position indication shall be included when specified in the applicable specifica-
tion sheet. Visual position indication shall consist of markings stamped or
engraved in an area adjacent to the driven component's openings (such as switch
covers or-actuator bodies) and a pointer stamped or engraved in or attached to the
driven component. Position identification markings shall be provided as specified
(see 6.2).
3.5.12.1 Electrical postion indication.
Remote electrical position
indication shall consist of sensitive switches mounted on the actuator body.
Moving parts shall be fitted with covers or guards to prevent equipment damage and
personnel injury. Unless otherwise specified herein, sensitive switches shall be
in accordance with MIL-S-8805.
3.5.13 Shims. Shims may be used as required to adjust shaft rotational
travel. Adjustments due to shimming shall not exceed 2 degrees. If shimming is
used, allowance shall be made for minimum thread engagement, where applicable.
Non-metallic shims shall be installed in actuators where galvanic action may occur
between the shims and surrounding material.
3.5.14 Mounting. The mounting interface configuration shall be as specified
in the applicable specification sheet
For Category I actuators, unless otherwise
defined by the specification sheet, the missing tooth on the rotating shaft spline
shall be in the position shown when the actuator is at the midpoint of the
required rotation angle
If a different alignment is required, the actuator
becomes Category II and the required alignment must be specified (see 6 2)
3.6 Operational environment
The following operational requirements shall
be in accordance with MIL-STD-2193:
(a)
Ambient temperature.
(b)
Shock (see 4.6.6).
(c)
Vibration (see 4.6 8).
(d)
Salt fog (see 4.6.10)
3.7 Material finishes
Surface roughness shall be determined in accordance
with ANSI B46 1 and shall be as specified in 3.7.1 and 3.7 2
3.7.1 External finishes
External surface finishes shall not exceed 250
microinches, except castings, which shall be as cast, External surfaces shall be
smooth, free of burrs, sharp edges, and other irregularities
For Parts Inquires call Parts Hangar, Inc (727) 493-0744
© Copyright 2015 Integrated Publishing, Inc.
A Service Disabled Veteran Owned Small Business