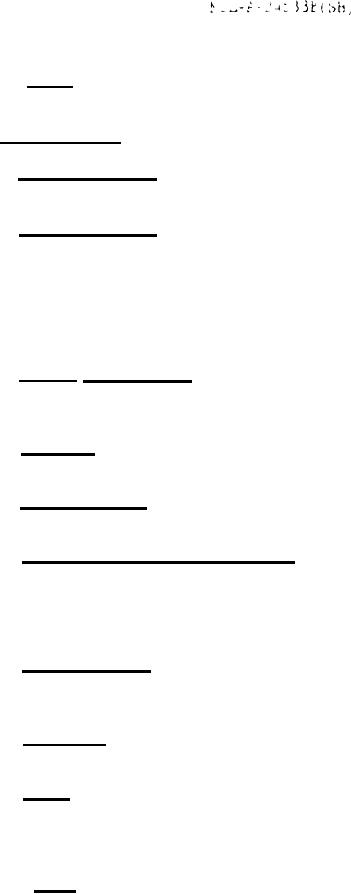
3 4.12 Noise. The actuators shall not exceed the allowable structureborne
noise Limits specified (see 6.2)
3 5 Construction ,
3.5.1 Actuator bodies. Unless otherwise specified herein, actuator bodies
shall comply with the general construction requirements of MIL-STD-2193.
3.5 2 Aluminum bodies. Actuators with an output greater than 136 newton
meter (N m)(l,200 inch-pound in-lb)) at rated operating pressure that utilize
aluminum as the body material shall be furnished with a corrosion-resistant
replaceable sleeve to separate the piston from the aluminum body to prevent
galling, corrosion, seizing, or excessive wear of the aluminum body. Exterior
surfaces of actuator aluminum bodies shall be anodized in accordance with MIL-A-
8625 and painted as specified in 3.7.3.
Brazing shall not be used in fabrication of
3.5.3 Welding and brazing.
actuator parts subject to hydraulic pressure. Welding requirements shall be in
accordance with MIL-STD-278, class M.
3.5.4 Chamfers. Methods of undercutting and chamfering for seal lead-in
shall be in accordance with MIL-G-5514.
3.5.5 Internal porting.
Transfer of hydraulic fluids across the actuator
shall be by internal porting within the actuator.
3,5.6 Relief ports and relief valves. Unless otherwise specified (see 6.2),
rotary actuators that require a sealed, fluid-filled gear chamber shall be
equipped with a relief valve or other pressure-limiting device. The operating
requirements of the relief valve shall be in accordance with the applicable
specification sheet or as specified (see 6.2).
3.5.7 Actuator ports. Actuator ports shall be in accordance with the
applicable specification sheet or as specified (see 6.2)
Tapered pipe threads
such as NPT are not permitted.
3 5.8 Fasteners.
Fasteners shall be in accordance with the requirements of
MIL-STD-2193.
3.5.9 Shaft. Actuator shaft shall be as specified in the applicable
specification sheet. Deviation from the specified shaft is permitted for category
II actuators provided it does not change the shaft bearing size or mounting
configuration of the qualified actuator.
3.5.10 Bearings. Antifriction or journal bearings shall "De selected from
the preferred-for-design series listed in MIL-STD-1762. The maximum design
bearing loads shall not exceed the basic dynamic capacity rating (capacity for one
million revolutions) of the bearing used.
6
For Parts Inquires call Parts Hangar, Inc (727) 493-0744
© Copyright 2015 Integrated Publishing, Inc.
A Service Disabled Veteran Owned Small Business